Разработка и производство медицинских ортопедическихизделий в компании ОРТО.НИК
Общие площади производственных помещений компании
На территории расположились стелечный и швейный цеха
Общее число постоянных рабочих
Наше производство располагается в самом центре Санкт-Петербурга, в здании легендарного предприятия «Красная нить». Более 170 лет эта мануфактура является хранителем традиций российского текстильного производства, и сегодня мы продолжаем эту богатую историю, создавая уникальные ортопедические изделия.
Орто.Ник - это компания полного производственного цикла, объединяющая все этапы создания ортопедических изделий под одной крышей. Мы гордимся тем, что контролируем каждый этап: от разработки и закупки материалов до выходного контроля качества, маркетингового сопровождения и постпродажной поддержки.
Разработка и производство медицинских
ортопедических изделий в компании ОРТО.НИК
Логистическая сеть Орто.Ник обеспечивает своевременные поставки материалов от проверенных поставщиков и оперативную доставку готовой продукции. Мы создали эффективную систему складского хранения с оптимальной ротацией товаров и быструю сервисную поддержку для наших клиентов.
Качество и надежность - главные принципы нашей компании. Каждое изделие проходит многоступенчатый контроль качества, что гарантирует безупречное исполнение и долговечность продукции.
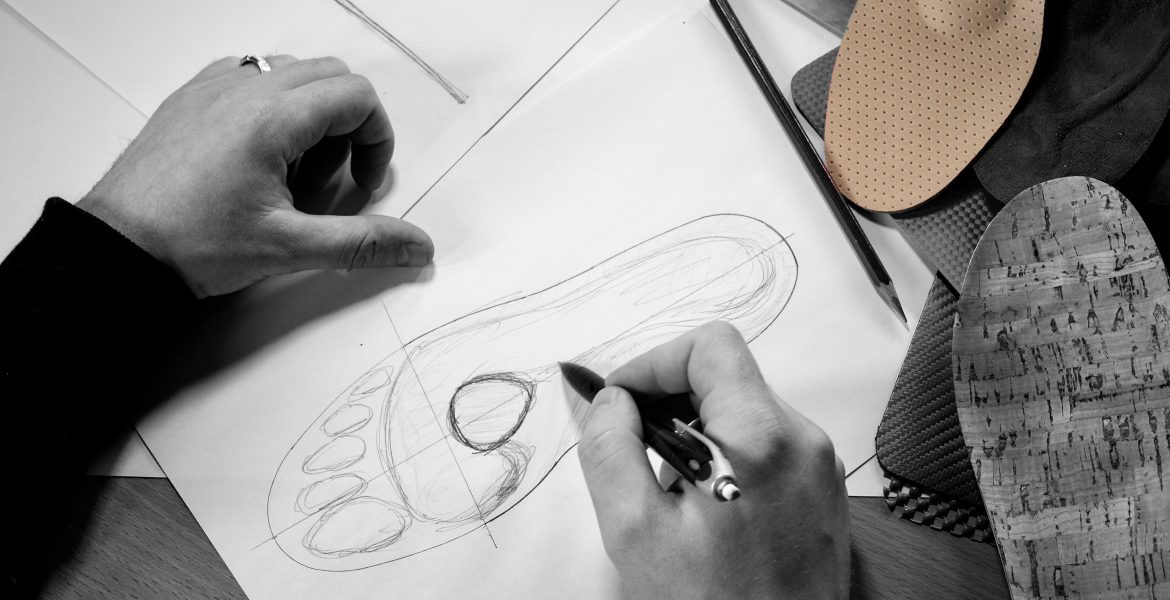
От идеи до продукта
за 1.5-2 года
Разработка медицинского изделия – сложный и многоэтапный процесс,
который требует времени
Производство любого изделия начинается с его разработки, а разработка начинается с анализа потребностей покупателей, работы конкурентов и состояния российского и международного ортопедического рынка. Так, в процессе сбора информации, дискуссий, консультаций с партнерами и врачами-ортопедами «рождается» идея нового медицинского изделия.
Затем к процессу подключаются инженеры-конструкторы и технологи. Для каждого изделия подбираются свои материалы и комплектующие, технологии производства и оборудование.
В каждом цехе несколько производственных участков
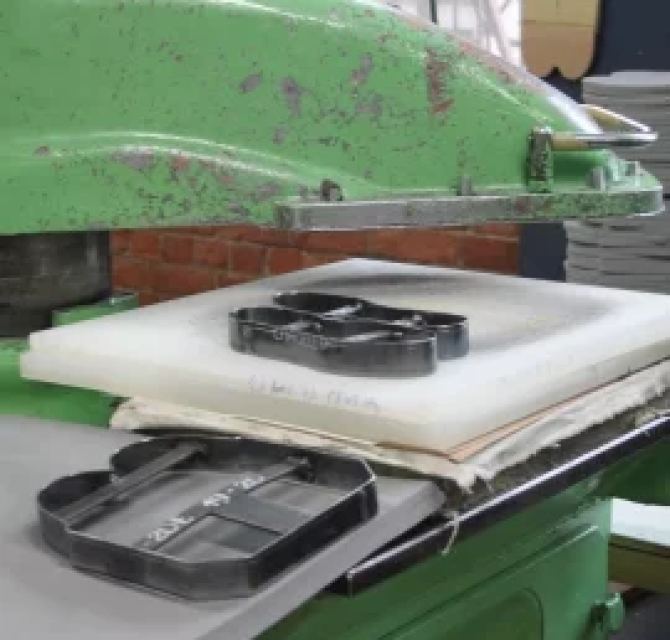
Раскройный участок
Производится автоматизированный раскрой материалов путем вырубки резаками -штанцами для соблюдения точной конфигурации на прессе ПВГ.
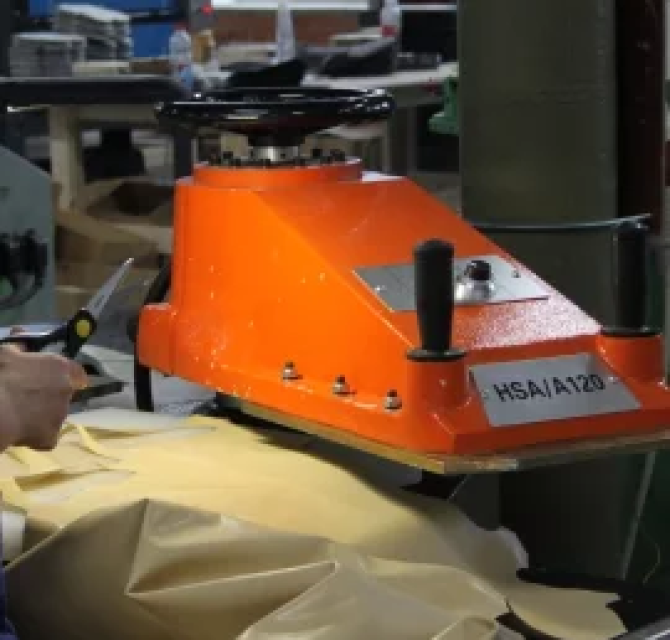
Участок вырубки и обработки кожи
Производится сортировка входящего сырья, двоение по толщине, обработка для более мягкого края, тиснение кожи для формирования рисунка и перфораций, который создает дополнительный эффект –микромассаж, воздухопроницаемость , мягкость.
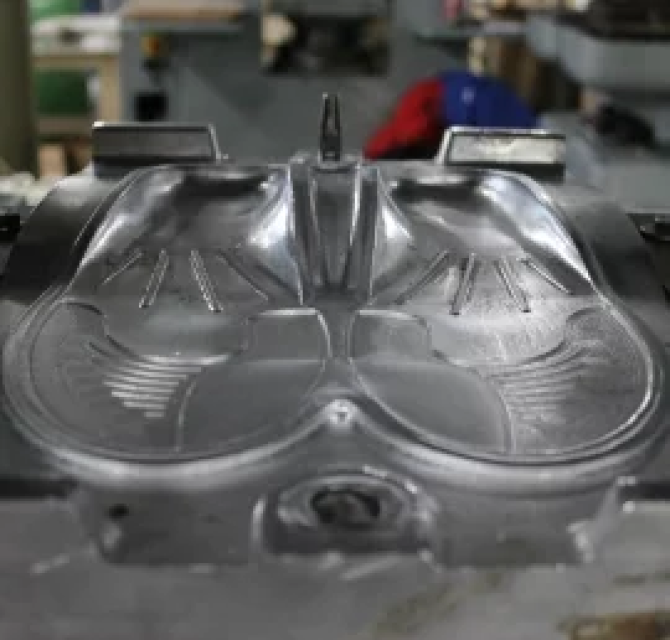
Участок горячего формования
Работа с пенополиуретанами (ППУ) на прессах с высокой температурой (170 градусов) для придания формы. Эта технология дает возможность сохранить мягкость ППУ и использовать дополнительные элементы при формовании (каркас для жесткости, амортизирующие и корригирующие вставки).
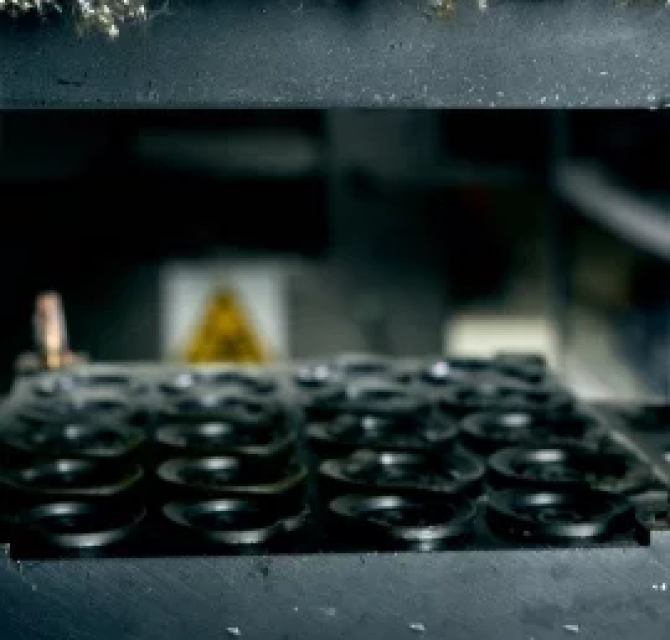
Участок холодного формования
Работа с EVA и термопластами. Процесс происходит в два этапа. Первый – разогрев материалов в печи, второй – формование в прессе с охлаждением заготовки. На выходе получается изделие необходимой жесткости, точно повторяющее заложенную конструктором форму.
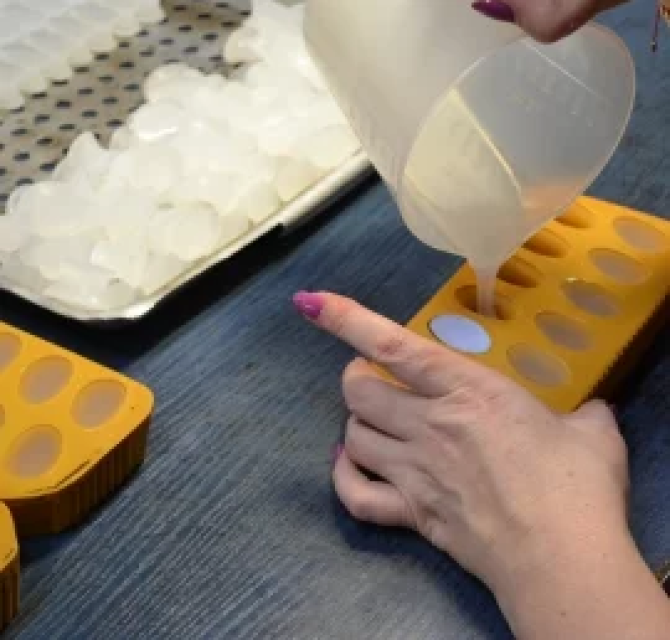
Участок литья силиконов
Функционирует как в автоматическом режиме (пласт-автомат), так и в ручном — литье в пресс-формы.
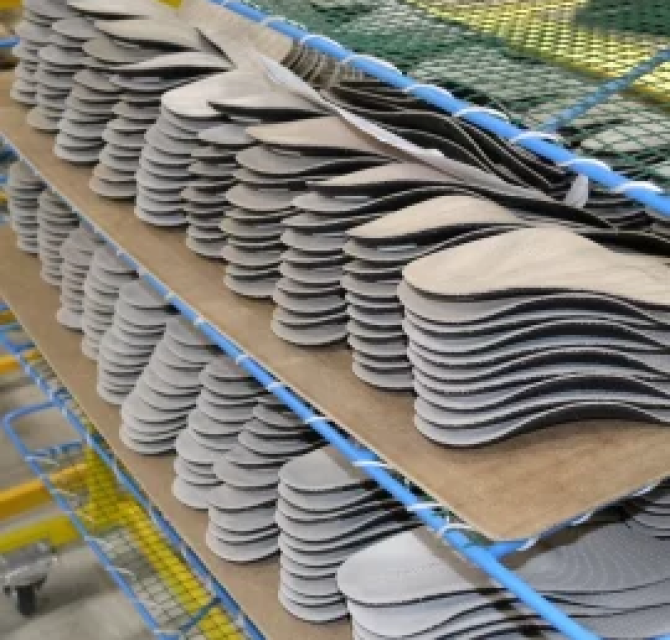
Сборочный участок
Функционирует в формате индивидуально изготовления. Участок оснащен вакуумными и мембранными прессами для закрепления клеевых соединений и для формования изделий на колодках. Также используются прессы для сборки и подформовки изделий с заданной конфигурацией каркаса и вырубные прессы для придания изделию товарного вида.
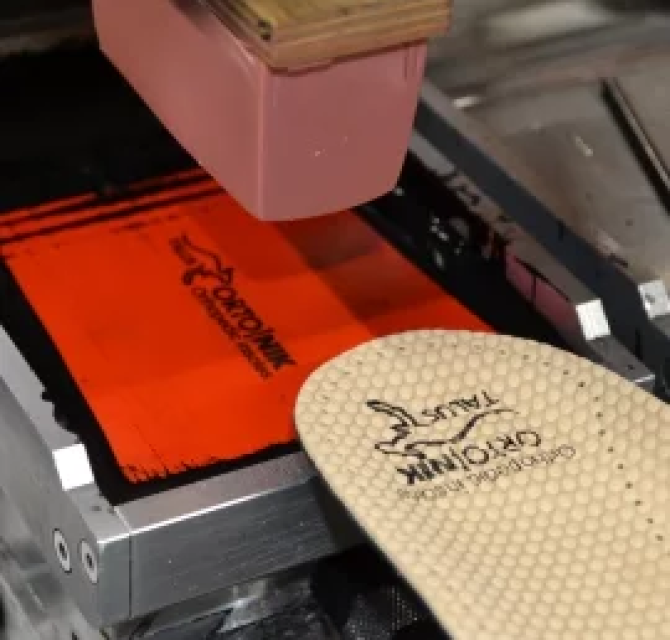
Участок клише
Здесь на готовое изделие наносится логотип методом тампонной печати. На кожаных стельках используется термопечать – тиснения под воздействием температуры.
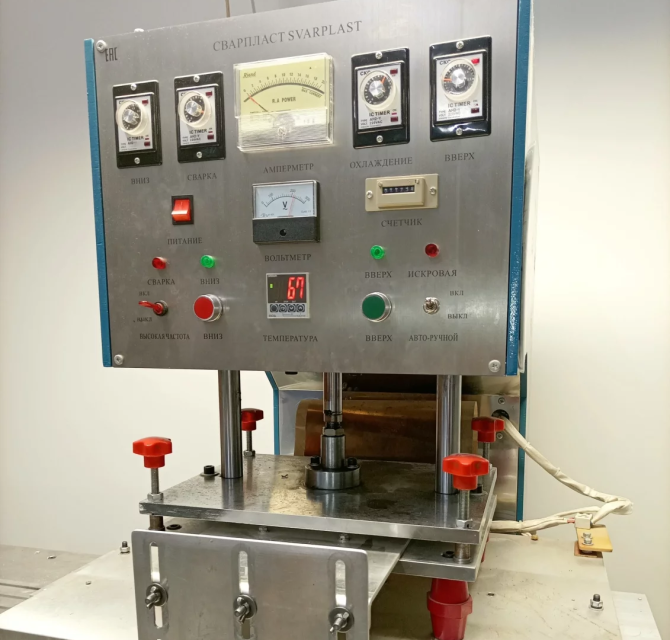
Участок ТВЧ
На этом участке проходят работы по «свариванию» заготовок на станке с применением токов высокой частоты (ТВЧ) — это застежки и замысовки для изделий из ассортимента «Бандажи и корсеты на туловище и на конечности».
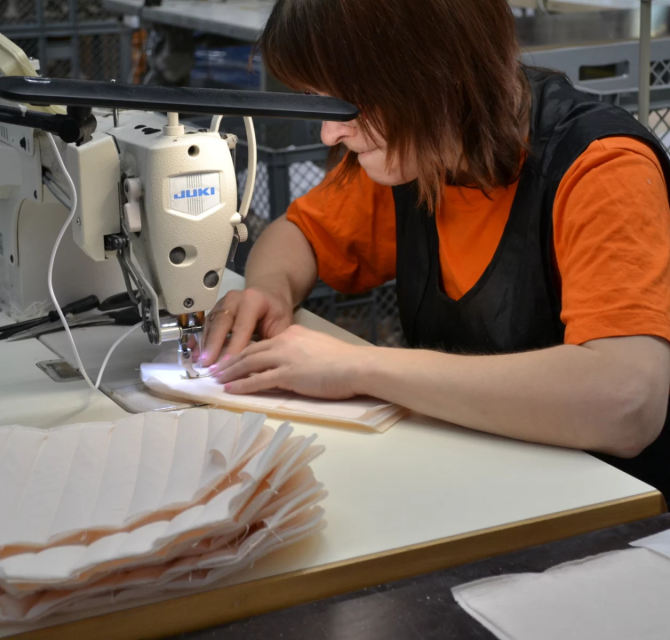
Швейный участок
имеет поточное производство по изготовлению продукции: корсеты на туловище (реклинаторы и противорадикулитные), бандажи на туловище, шейные воротники, бандажи на нижние конечности. Каждые поток имеет свои виды оборудования — машины цепного стежка, двухигольные машины для настрачивания лент и тесьмы, машины распошивальные с эластичными бельевыми швами.
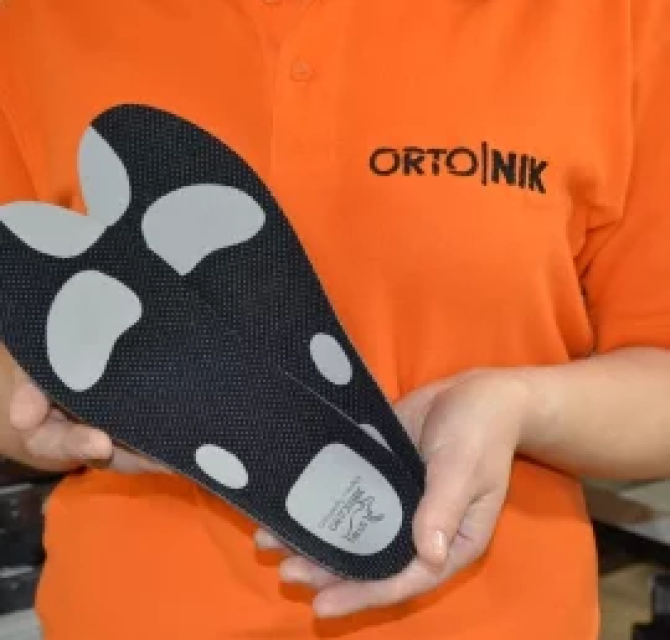
Участок контроля качества
проверяются все материалы и комплектующие при поступлении, проходят промежуточный контроль все полуфабрикаты. Также выходной контроль качества проходят все произведенные нами изделия. Совместно с технологами проводится регулярное тестирование каждой партии изделий по параметрам, предъявляемым ГОСТами к ортопедическим изделиям.
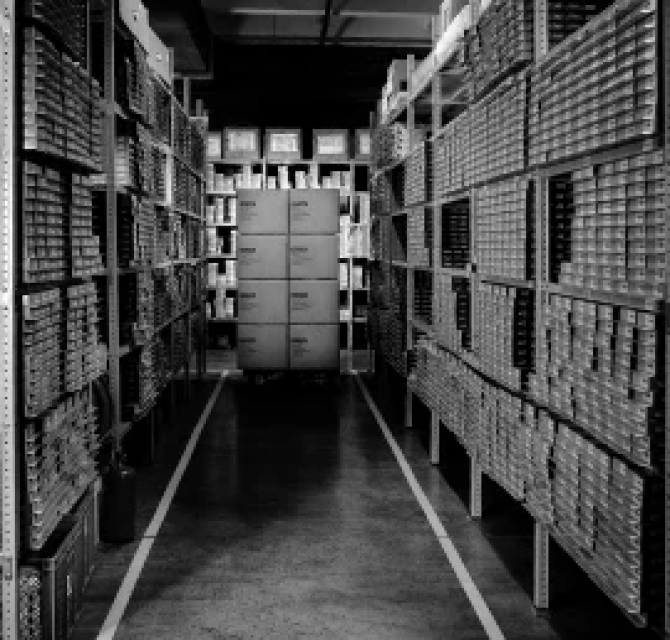
Склад готовой продукции
площадь около 700 м3 и хранится более 460 наименований изделий. Ежедневно в среднем мы отгружаем медицинские изделия в 27 торговых точек с охватом всех регионов России и ближнего зарубежья.